What is Quality Assurance? Definition and Importance
Quality assurance (QA) is a systematic way to make sure products and services meet quality standards. A comprehensive overview of the quality assurance definition reveals that it is a fundamental aspect of quality management that encompasses various sectors such as manufacturing and technology. QA plays a critical role in ensuring that products and services meet stakeholder expectations by implementing systematic processes to enhance quality and compliance while reducing costs and risks associated with defects. Think of QA as a safety net that catches problems before they reach customers.
Organizations worldwide follow standards set by ISO (International Organization for Standardization) - think of ISO as the global rulebook for how to do things right. ISO 9001, the most widely used quality standard, helps companies build reliable systems to deliver good results every time. ISO 9001 includes guidance on risk-based decision making.
The role of quality assurance helps companies in three key ways. First, it prevents mistakes by catching errors early in production. Second, it saves money by reducing waste and the need to redo work. Third, it makes customers happier by delivering better products.
Quality assurance has its own department in most companies and especially, tech departments. Quality assurance teams test products and services while writing clear testing rules. They train workers on quality standards and track problems until they’re fixed. Most importantly, they ensure everything follows industry rules and standards.
For example, A quality assurance test for website deployment will ensure the website’s accessibility, mobile-friendliness, responsiveness, etc.
The above example is a classic example of product-based QA. There’s a total of 4 types of quality assurance, which are:
- Product-based QA checks if items meet physical standards
- Process-based QA monitors how things are made
- System-based QA looks at the entire operation
- People-based QA focuses on worker training and skills
Companies need quality assurance because it protects both the business and its customers. Without QA, products might have problems that could hurt sales, damage the company’s name, or even harm users.
Quality Assurance vs. Quality Control: Key Differences
The difference between quality assurance and quality control is that Quality Assurance (QA) prevents problems before they occur, while quality control (QC) finds and fixes problems after they happen.
Quality assurance focuses on proactive planning and process improvement to prevent risks that could affect product or service quality. It creates the rules and systems that help make products right the first time. It trains workers, sets up proper procedures, and designs efficient workflows. Quality control, on the other hand, is more reactive and seeks to identify defects after production, stepping in at the end to test products and catch any defects that slipped through.
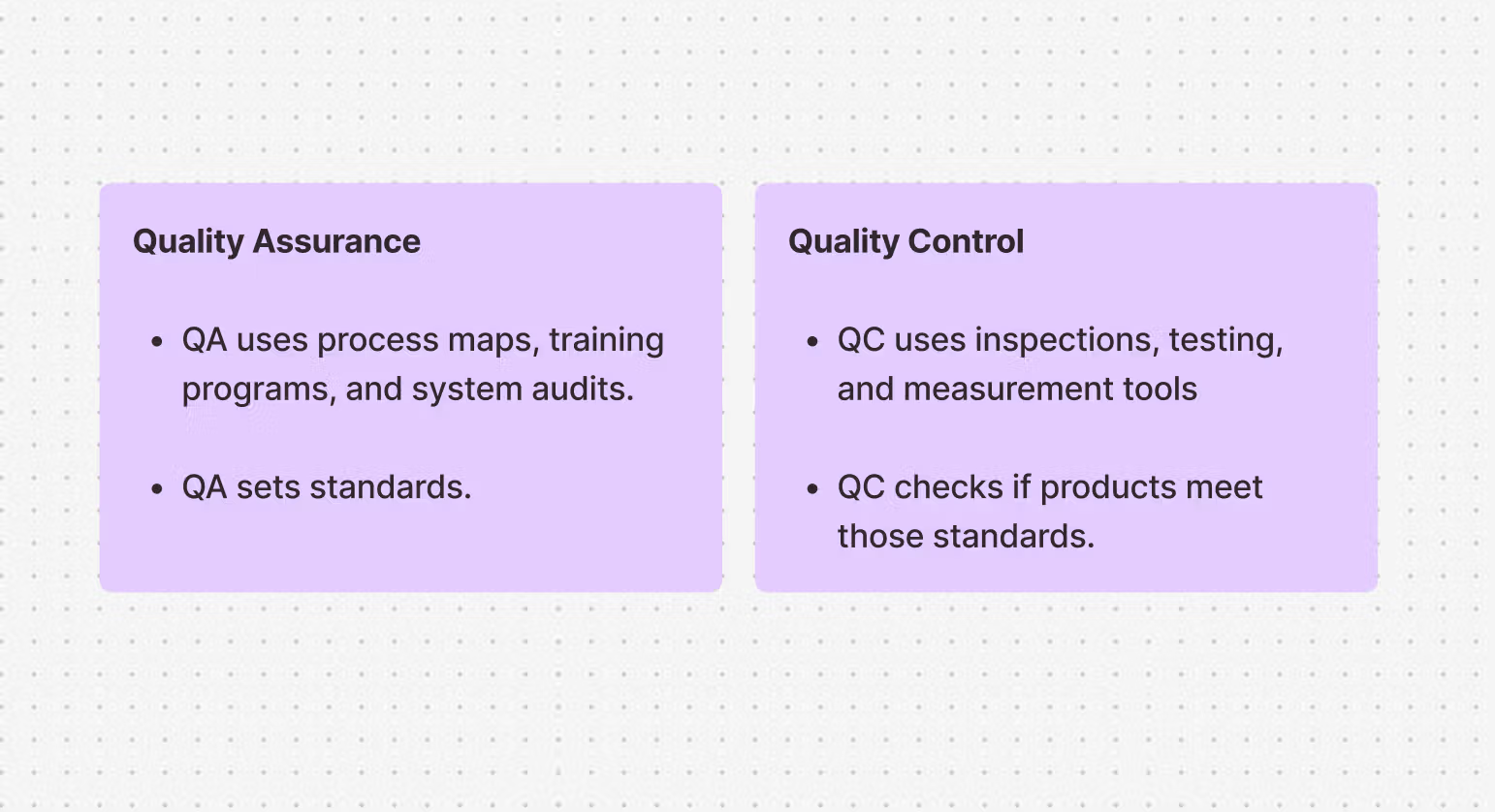
While both QA and QC aim for quality products, they work best when used together.
Quality Assurance Process
A quality assurance process works in five main steps:
- Set clear quality goals
- Create a detailed plan
- Test everything thoroughly
- Watch and fix problems
- Learn from results
Implementing a quality assurance system is crucial for establishing organizational credibility and enhancing operational efficiency. Such systems, particularly those aligned with ISO standards like ISO 9001, promote compliance, transparency, and continuous improvement in businesses, especially within regulated industries.
First, set quality standards that match what customers want. Think about it like making rules for a game - everyone needs to know what counts as “winning.”
Next, make a plan that shows who does what. This plan tells your team when to check things and what tools to use, just like a recipe tells you when to add each ingredient.
Then, test everything to find problems. Testing works like trying out a new bike before buying it - you want to make sure everything works right.
After testing, watch how things work and fix any problems fast. It’s like being a referee in a game - you watch closely and call out when something’s wrong.
Last, write down what you learned. This helps make things better next time, like taking notes in class helps you do better on the next test.
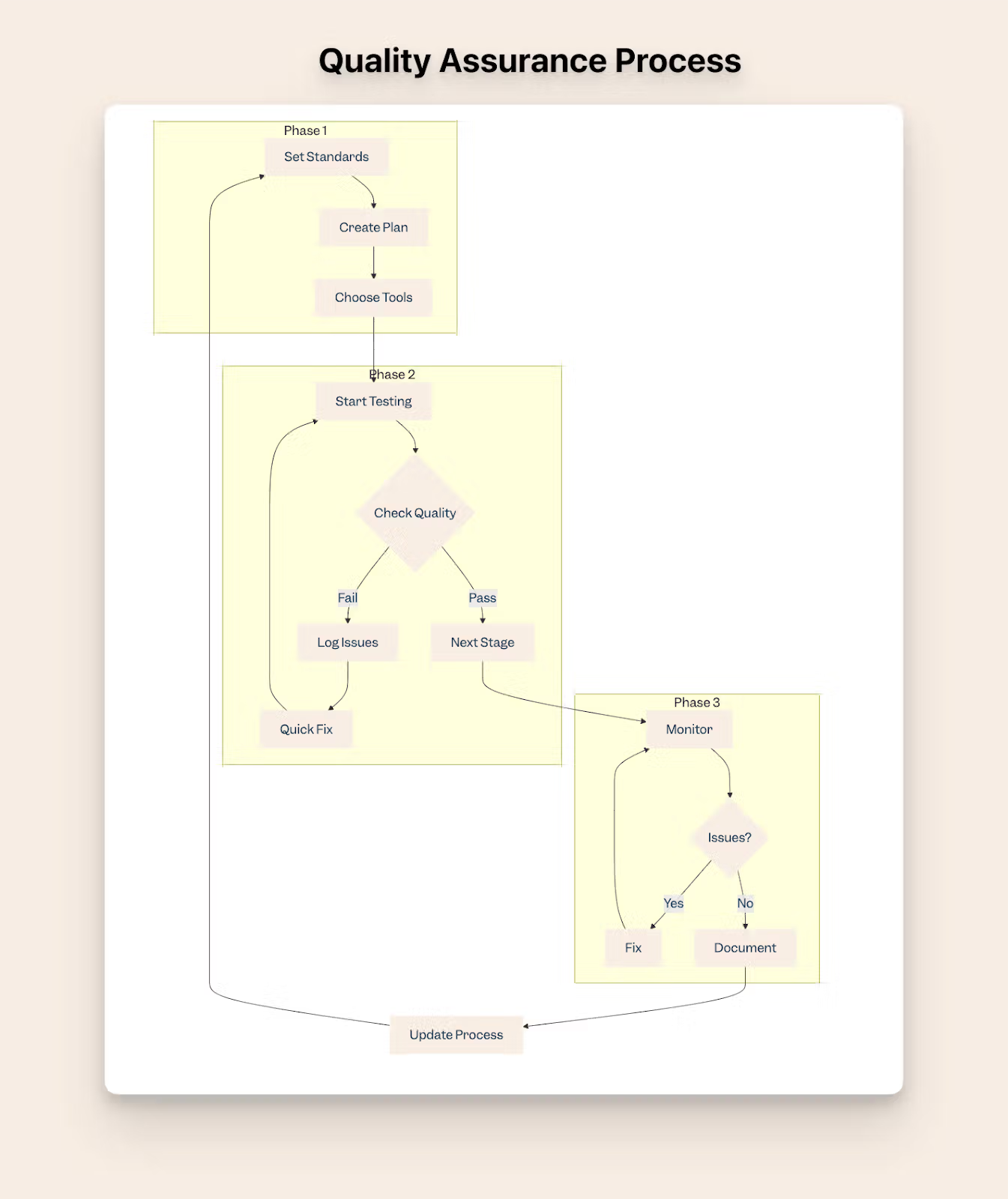
Good quality assurance means fewer mistakes, happier customers, and less wasted time and money. When teams follow these steps, they make better products and keep getting better at what they do.
Quality Assurance Methods
Quality assurance methods are systematic approaches used to prevent defects and ensure consistent product quality. These methods work together to verify that products and services meet defined standards, satisfy customer requirements, and maintain reliability throughout their lifecycle.
Key QA methods include:
- Total Quality Management (TQM)
- Failure Testing
- Process and Product Quality Assurance (PPQA)
- Capability Maturity Model Integration (CMMI)
- Statistical Process Control (SPC)
Total Quality Management (TQM)
TQM is a company-wide approach that makes quality everyone’s responsibility. Implementing systematic practices to avoid defects and ensure customer satisfaction is crucial, highlighting the role of continuous improvement in achieving high service quality standards. It focuses on long-term success through customer satisfaction, involving all members of the organization in improving processes, products, services, and the culture they work in. Teams work together to prevent problems before they occur rather than fixing them after.
Failure Testing
Failure testing deliberately pushes products to their limits to identify weaknesses. This method includes stress testing, load testing, and accelerated life testing to find potential breaking points before customers do. By understanding how and why products fail, companies can improve design and prevent future problems.
Process and Product Quality Assurance (PPQA)
PPQA evaluates both the manufacturing process and the final product against established standards. It ensures that production methods follow documented procedures and that finished products meet specifications. This dual focus helps catch issues at their source while verifying the quality of completed items.
Capability Maturity Model Integration (CMMI)
CMMI provides a framework for process improvement across an organization. It defines five maturity levels, from initial to optimizing, helping organizations understand their current capabilities and plan improvements. This method creates a roadmap for developing better products and services through improved processes.
Statistical Process Control (SPC)
SPC uses statistical methods to monitor and control processes. By collecting and analyzing data, teams can identify variations that might affect product quality. This method helps distinguish between normal process variations and serious problems that need attention, enabling data-driven decision making.
Quality Management
A Quality Management System (QMS) provides a structured approach to managing quality through documented policies, procedures, and processes that ensure consistent delivery of products and services meeting customer expectations.
Quality Management System (QMS) Components
Every effective QMS consists of three core elements:
- Quality Policy: The organization's overall intentions for quality
- Quality Objectives: Specific, measurable quality goals
- Quality Manual: Detailed documentation of procedures and processes
Building Your QMS with Slite
Creating and managing a QMS doesn't have to be complicated. Slite offers a simple, team-friendly knowledge base solution that makes QMS documentation accessible and maintainable.
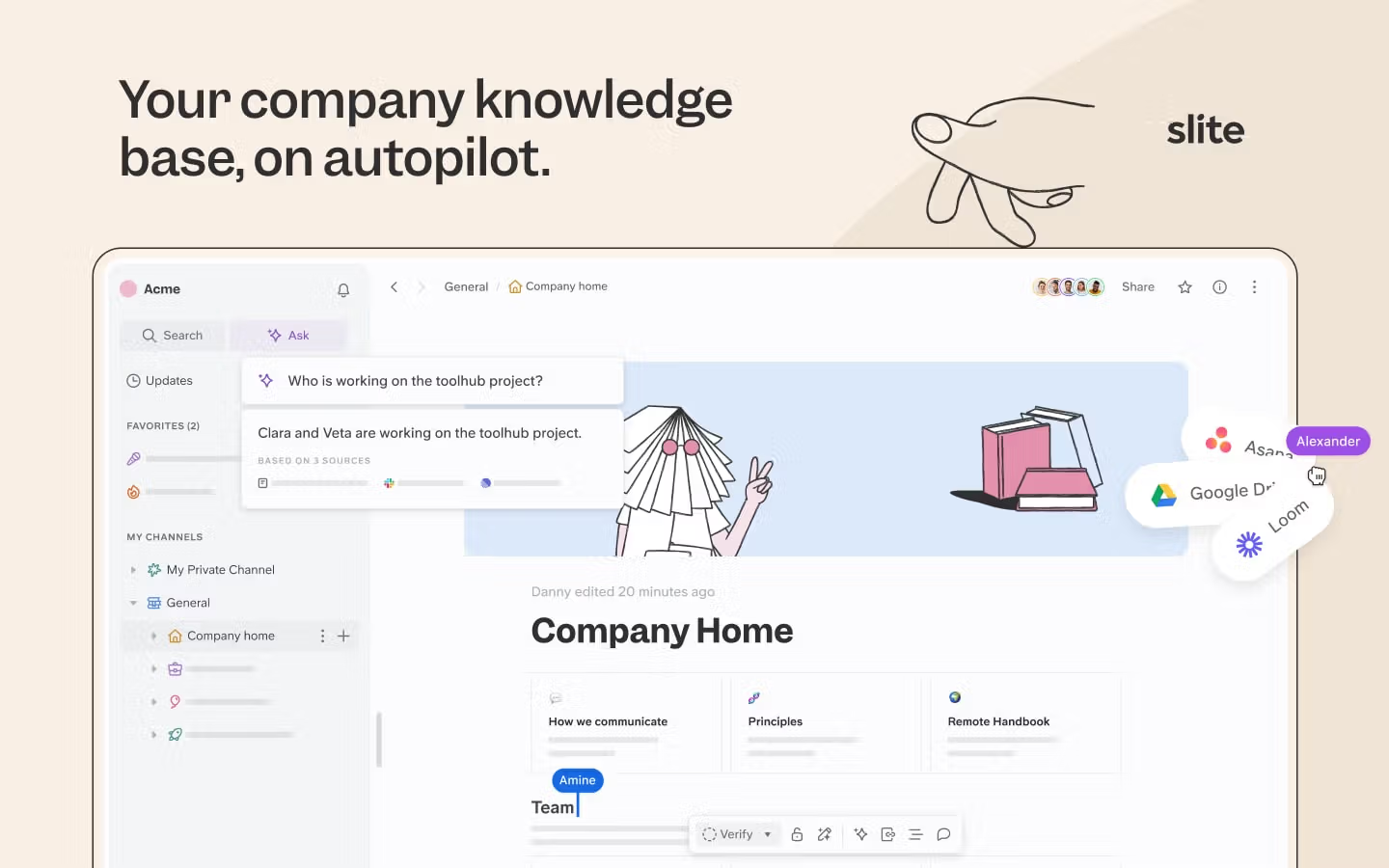
The best part is, with Slite, you don't even have to manually build your QMS. You can use Slite's AI wiki generator to build your QMS via simply chatting with AI. For example,

You can generate structured quality policies, share documentation instantly, and maintain a searchable repository of quality procedures. Team members can easily access, query, and update the QMS documentation, ensuring your quality system remains current and effective.
To get started, simply create a workspace in Slite, use the AI generator to draft your initial documentation, and share access with your team. The platform's intuitive interface makes it easy to maintain and update your QMS as your organization grows and evolves.
Industries That Benefit From Quality Assurance
Quality assurance plays a vital role across diverse industries, each adapting QA principles to their specific needs. While some organizations maintain internal QA teams, many successfully leverage external contractors or consultants for their quality assurance needs.
Key industries implementing QA:
- Software Development: Ensures reliable, secure, and bug-free applications. Emphasizes the importance of software quality assurance (SQA) in improving development cycles by systematically identifying errors and trends before they escalate, thereby saving time and costs. Discusses various SQA models and methodologies, underscoring how SQA can be integral to software development strategies like Agile and Waterfall, while also addressing challenges such as potential regressions caused by fixes.
- Manufacturing: Maintains product consistency and safety standards
- Healthcare: Guarantees patient safety and regulatory compliance
- Finance: Protects data accuracy and transaction security
- Aerospace: Ensures equipment reliability and safety
- Food and Beverage: Maintains product safety and consistency
- Education: Maintains academic standards and program quality
Roles and Responsibilities in Quality Assurance
Quality Assurance involves a team effort, with various roles and responsibilities crucial to its success. Here are some key roles and responsibilities in QA:
- Quality Assurance Manager: The QA Manager oversees the entire QA process, ensuring that quality objectives are met and implementing quality management systems. They are responsible for setting quality standards, developing QA policies, and leading the QA team to achieve organizational goals.
- Quality Assurance Engineer: The QA Engineer designs and implements QA processes, conducts testing and validation, and identifies areas for improvement. They work closely with development teams to ensure that quality is built into the product from the start, using various quality assurance methods and tools.
- Quality Assurance Analyst: The QA Analyst analyzes data, identifies trends, and provides insights to improve the QA process. They monitor quality metrics, conduct root cause analysis, and recommend corrective actions to enhance product quality and customer satisfaction.
- Quality Assurance Tester: The QA Tester is responsible for testing products or services, identifying defects, and reporting issues. They execute test cases, document test results, and work with developers to resolve any problems, ensuring that the final product meets quality standards.
- Quality Assurance Specialist: The QA Specialist ensures that products or services meet quality standards, conducts audits, and implements corrective actions. They review processes, perform inspections, and verify compliance with quality requirements, contributing to the overall effectiveness of the quality management system.
These roles and responsibilities work together to ensure that the QA process is effective, efficient, and aligned with organizational goals. By collaborating and leveraging their unique skills, the QA team can drive continuous improvement and deliver high-quality products and services that meet customer expectations.
Best Practices in Quality Assurance
The five most important quality assurance best practices help teams deliver better products and services. These key practices focus on documentation, training, reviews, feedback, and data - making quality everyone's responsibility.
ISO standards, particularly ISO 9001, provide internationally recognized frameworks for quality management systems. These standards help organizations consistently meet customer requirements and enhance satisfaction. So without waiting further, let's check out the best QA practices:
Clear Documentation and Processes
Good documentation helps everyone do quality work correctly. ISO 9001 specifically requires documented information to support process operations and demonstrate effective quality management. Teams need easy-to-follow guides that explain exactly what to do and how to do it. When processes change, the documentation must change too. This keeps everyone on the same page and prevents mistakes that could affect quality.
That's where Slite comes in - we're a Knowledge Base that you'll actually love using.
Slite has one of the highest G2 scores for ease-of-use, has all the essential features you'd need in a top Knowledge Base without feeling cluttered of overwhelming.
Regular Training and Development
Teams need training to maintain high quality standards. Regular workshops teach both technical skills and quality awareness. When team members understand quality processes well, they make fewer mistakes and spot problems early. Training keeps everyone sharp and ready to handle quality challenges.
Systematic Audits and Reviews
Regular quality checks catch problems before they grow. Teams should review their work often and invite outside experts to look at their processes. These reviews show what's working well and what needs fixing. When teams fix problems found in audits, quality improves quickly.
Customer Feedback Integration
Customer feedback shows if quality efforts are working. Teams should ask customers what they think and use their answers to make things better. Good feedback systems include surveys and interviews. When teams listen to customers, they know exactly what needs improvement.
Data-Driven Decision Making
Numbers tell the true story about quality. Teams should track their quality performance and use real data to make decisions. When teams measure their work, they can spot trends and fix issues early. Data helps teams prove their quality is improving and shows where to focus next.
Future of Quality Assurance
Quality assurance is changing fast as new technology transforms how we ensure quality. Smart tools and new ways of working are making quality checks faster, more accurate, and more reliable.
AI and Machine Learning
Smart computers are changing how we check quality. AI can spot problems faster than humans and predict where issues might occur. Machine learning helps quality teams work smarter by learning from past data and suggesting better ways to test.
For example, Slite's AI search helps its customers get to answers via trusted company information much faster. In Slite's Search box, you don't type random keywords to look for documentation, instead you can ask specific questions and get answers from verified sources:
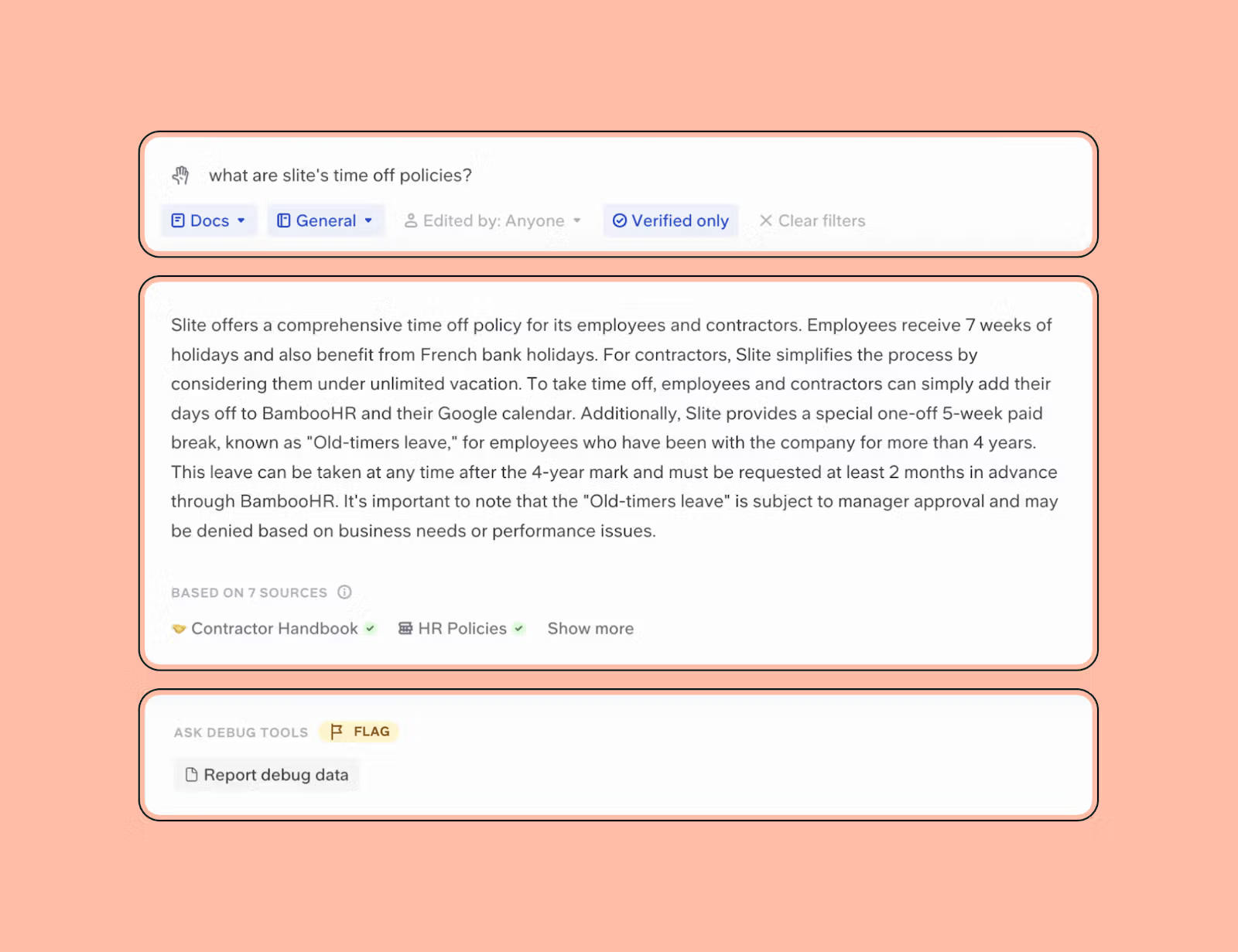
Cloud-Based Quality Tools
Teams now use cloud tools to manage quality from anywhere. These online platforms let everyone see quality data in real-time and work together easily. When quality tools live in the cloud, teams can share information quickly and fix problems faster. Plus, updates happen automatically, so everyone always has the latest tools.
Automated Testing
Robots and computers are taking over repetitive quality checks. Automated tests run faster and don't get tired or make mistakes like humans do. Teams can test more often and catch problems earlier when machines do the routine work. This lets quality experts focus on solving complex problems instead of doing basic checks.
Real-Time Quality Monitoring
New sensors and systems watch quality as things happen. Teams don't have to wait for reports - they can see problems right away and fix them immediately. Real-time monitoring helps prevent bad products from reaching customers. When teams can respond quickly, quality stays high and costs stay low.
Sustainable Quality Practices
Future quality work must protect both products and the planet. Teams are finding ways to ensure quality while using less energy and creating less waste. Green quality practices help companies meet environmental rules while still making great products. When quality work considers sustainability, everyone benefits.
Conclusion
Good quality assurance depends on both smart practices and modern tools. Teams need clear processes, regular checks, and the right technology to deliver quality consistently.
How Slite Supports Your Quality Journey
Slite makes quality documentation simple and clear. Your team can:
- Create and update quality guides quickly
- Share procedures instantly with everyone
- Track changes automatically
- Find important documents fast
- Get AI help writing and formatting docs
Quality work needs good tools backing it up. Think of quality like building a house - you need both skilled workers and the right equipment. Slite gives teams the tools they need to build and maintain quality practices that last.
Need help picking the right quality tools or making your processes better? Let's talk about how to make quality work easier for your team.